- Home
- Products
- Machines
- Sheet laser cutting machines
- Sheet laser cutting machines Active Tools
Excellence within everyone's grasp
Designed to ensure productivity, safety, quality, automation, and ease of use. Active Tools function automatically adjusting the working parameters to give you better results in less time.
Automatic nozzle change and wear monitoring function
Fully-automatic material and thickness changes for faster and error-free production, even in unmanned mode. An 18-position device will replace the nozzle whenever the new batch requires it. With the same device, wear and integrity is monitored and calibrated, all concentrated in one place for reliable results and a quick start to cutting.
Increases productivity on medium and thicker materials
Continuously monitors the quality and progress of each piercing operation until breakthrough to give you constant and reliable results throughout the entire process. In case of critical conditions and risk of losing the cut, the function intervenes, giving indications to resume the process in optimal conditions.
Change production without interruption
The focal position automatically adjusts based on the material type and thickness to produce optimal cutting results. There is no need for manual adjustments as Active Focus does the work for the work for you.
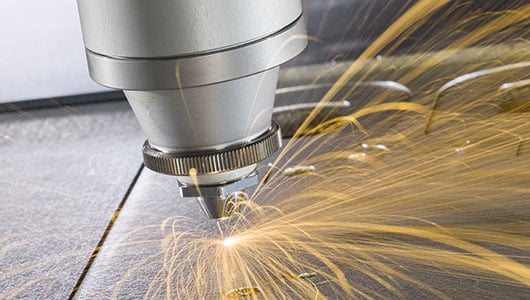
-70% faster for cutting grids
Making sequences of square and rectangular geometries in-line instead of one at a time gives you great productivity advantages. The operation of the laser switches on and off to precisely synchronize with the start and end position of all linear strokes to be cut, executed in sequence. The result means you can make entire rows of geometries very fast.
Using water improves quality
When cutting thick materials, water is emitted directly from the nozzle to dissipate the heat during cutting, to produce high-quality results, even when processing with high laser power and closely nested patterns.
Every thickness has its laser beam
The ability to change the diameter of the laser beam automatically provides optimum performance with all thicknesses. A smaller diameter beam with thinner materials to increase cutting speed and a larger diameter beam for thicker materials to improve the service gas flow and achieve a better and consistent cut finish.
Optimal cutting in all conditions
Active Speed rapidly produces the best cut quality on all material conditions. Automatic adjustments of all cutting parameters, even intricate patterns and geometries (sharp edges, teeth, micro close cuts), will be imperfection-free.
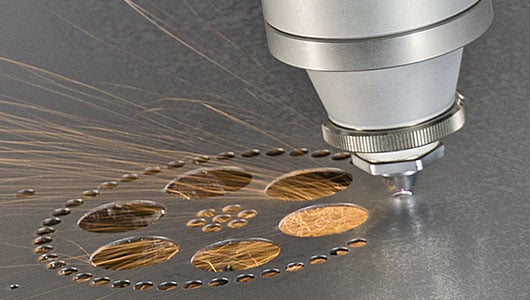
Assisted nozzle centering
All the help you need for occasional nozzle centering checks. Any deviation from the optimal position is measured and indicated to the operator who also receives instructions to quickly correct the detected condition and restart the system. The optical device integrated into the camera measures the installed nozzle by measuring its coaxiality with the laser beam necessary for the correct action of the service gas during the job.
Utilize every inch of material
You can quickly cut remaining parts and new parts even on the smallest sheet remnants. View the remnant from the operator console, drag a virtual outline of the part and drop it in place to utilize the available material.
The information when you need it directly in your inbox
Get information on machine status, updates on routine maintenance needs, notifications on the necessary interventions, all automatically from an email sent by the machine to the programmed addresses. You have access to the information quickly and can easily keep record.
No unexpected processing defects
With increased safety for unattended part processing, Active Sense automatically adjusts cutting parameters to compensate for variations in material thickness.
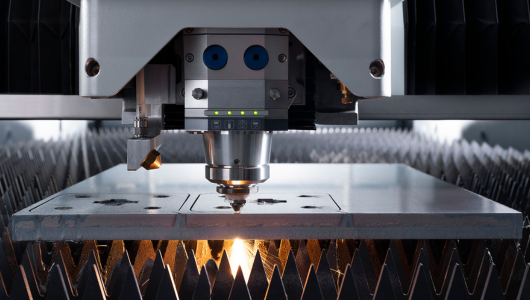
Activate your success
Learn more about Active Tools technology. Ask us what you want to know and find out how these features advance your production.
Many companies are already taking advantage of Active Tools to improve their production.
Don't get left behind!
Our machines can change your business
Learn how we have helped our customers realize their business goals through our solutions.
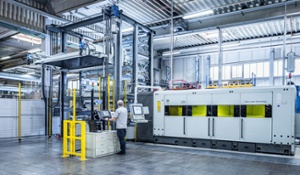
OEM
What he used to produce in two or three shifts, he now manages to do in one shift.
Find out how he did it.
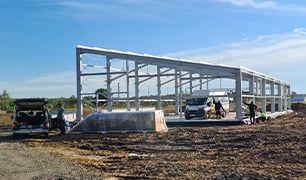
Structural
They combine tubes and beams of any cross-section in an innovative way, removing the complexity and variety of machining methods which represent an additional cost burden.
Find out how they do it.