Highlights
Areas of application
-
AUTOMOTIVE
-
MOTORCYCLES
-
AEROSPACE
-
FURNITURE
-
HVAC
-
INDUSTRIAL VEHICLES
-
STRUCTURAL
-
FITNESS
-
Domestic Appliances
-
SUBCONTRACTORS
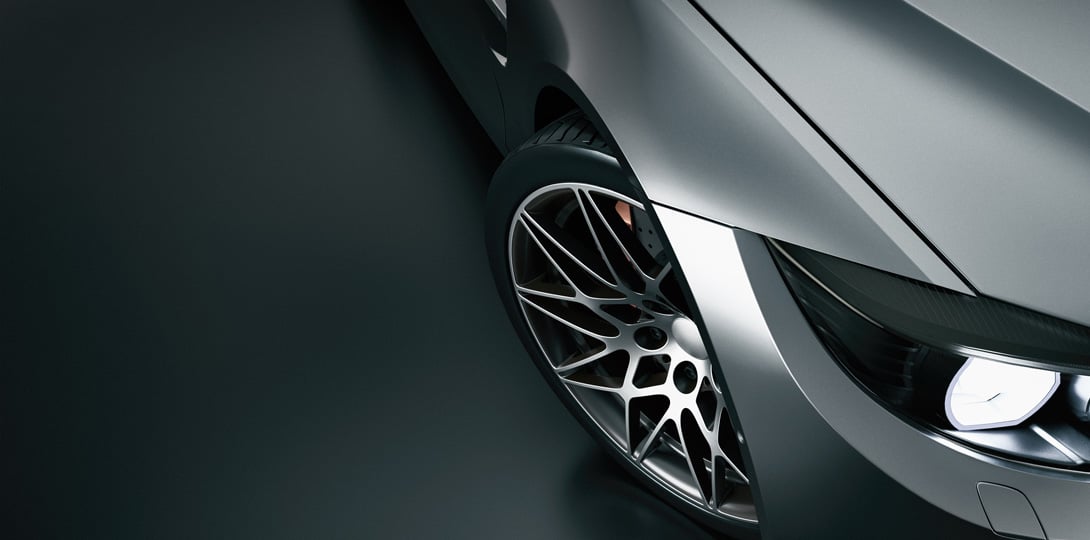
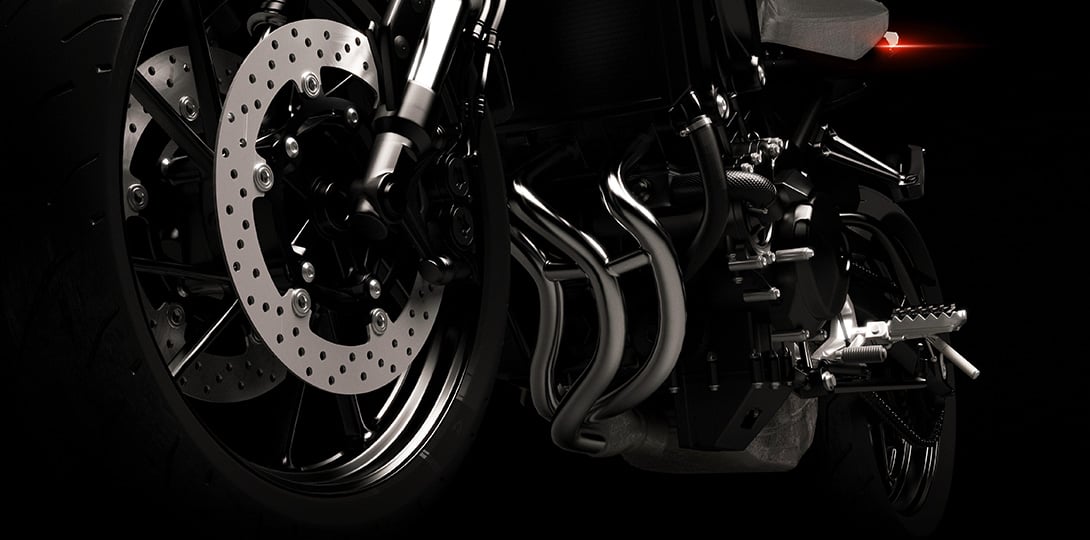
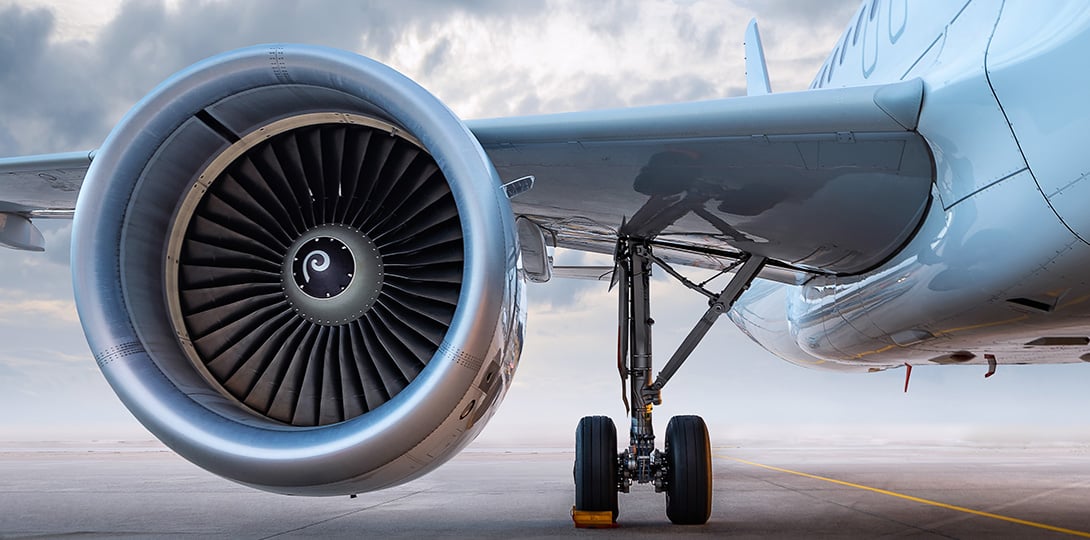
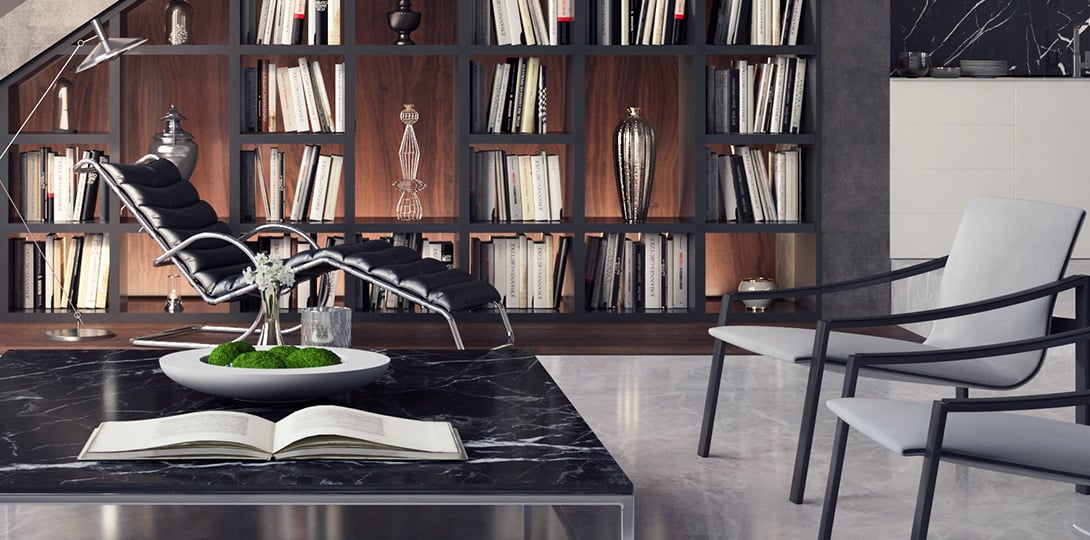
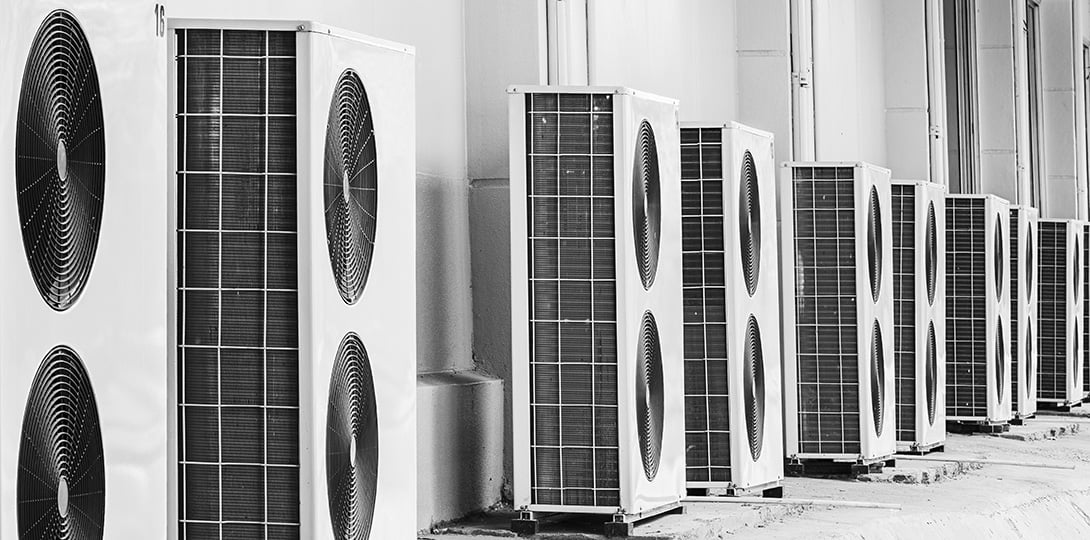
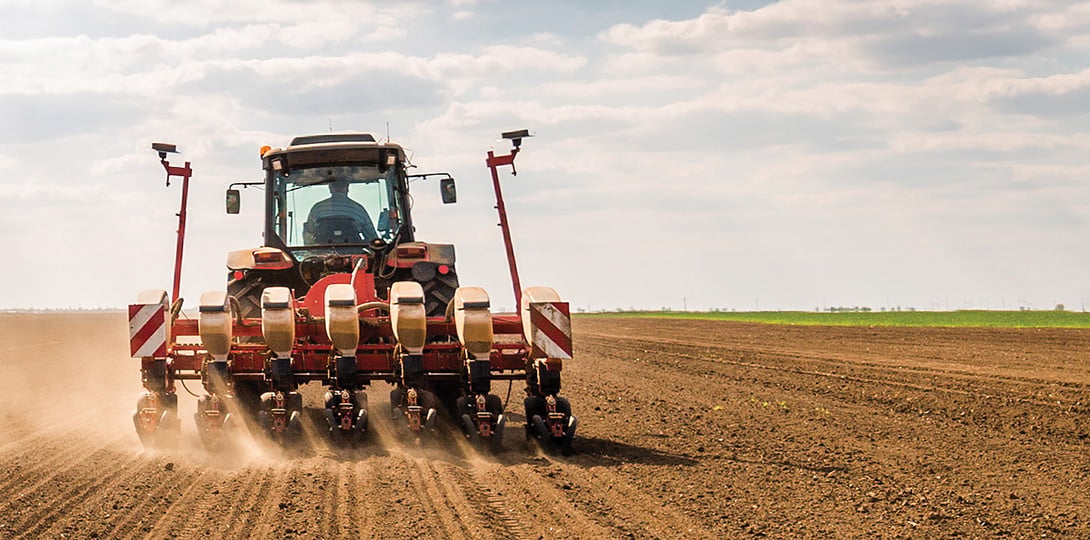
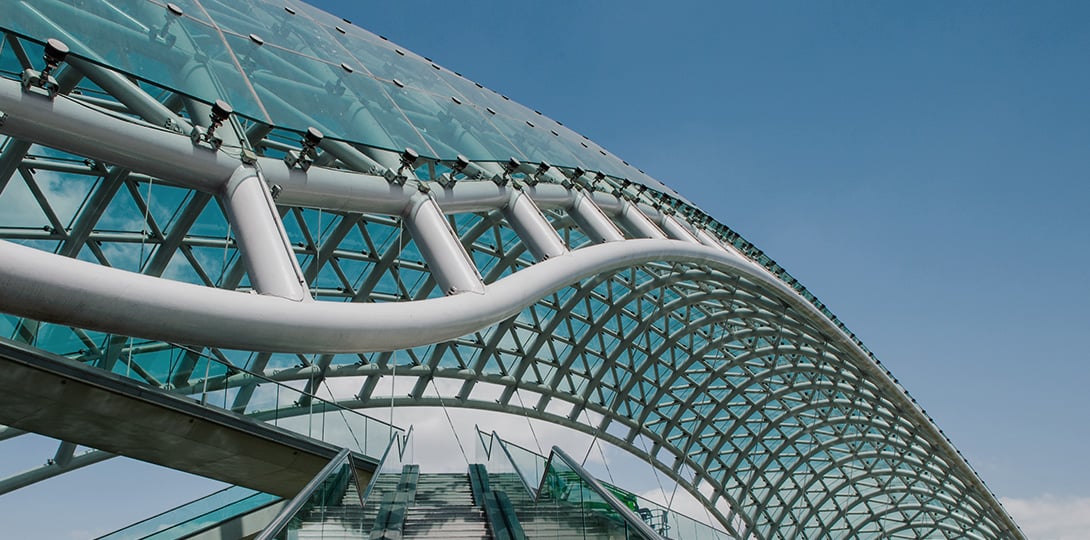
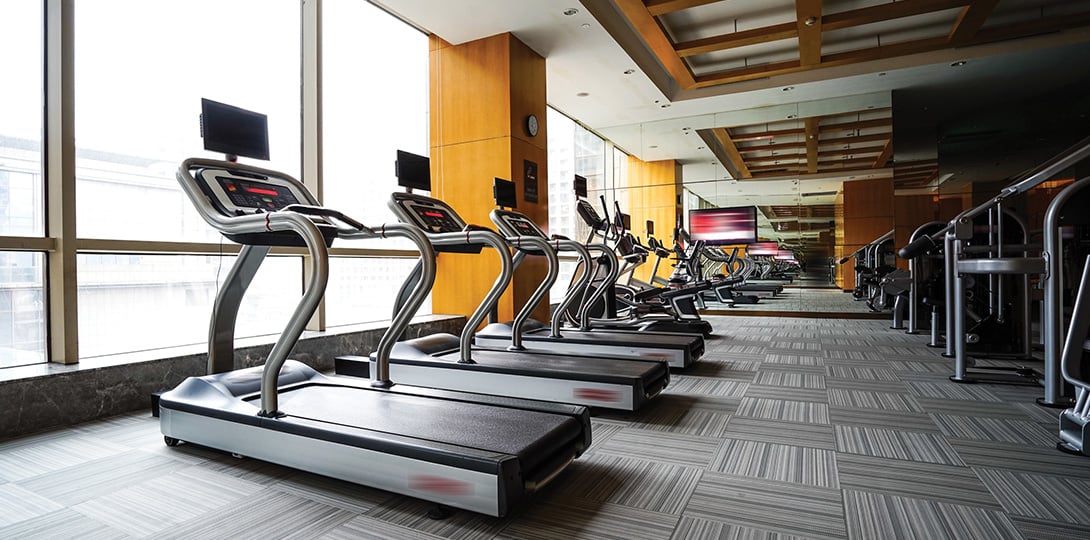
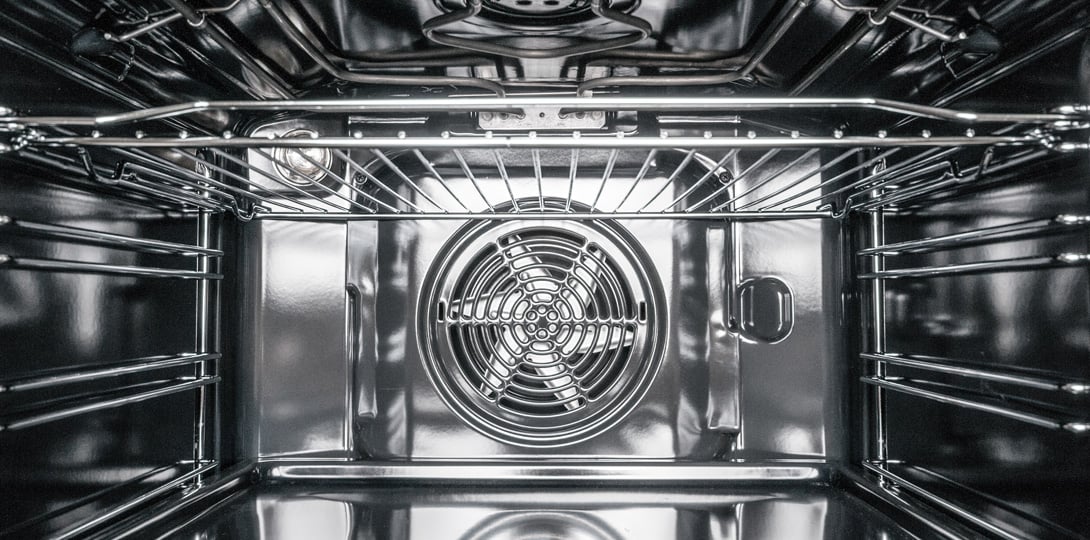
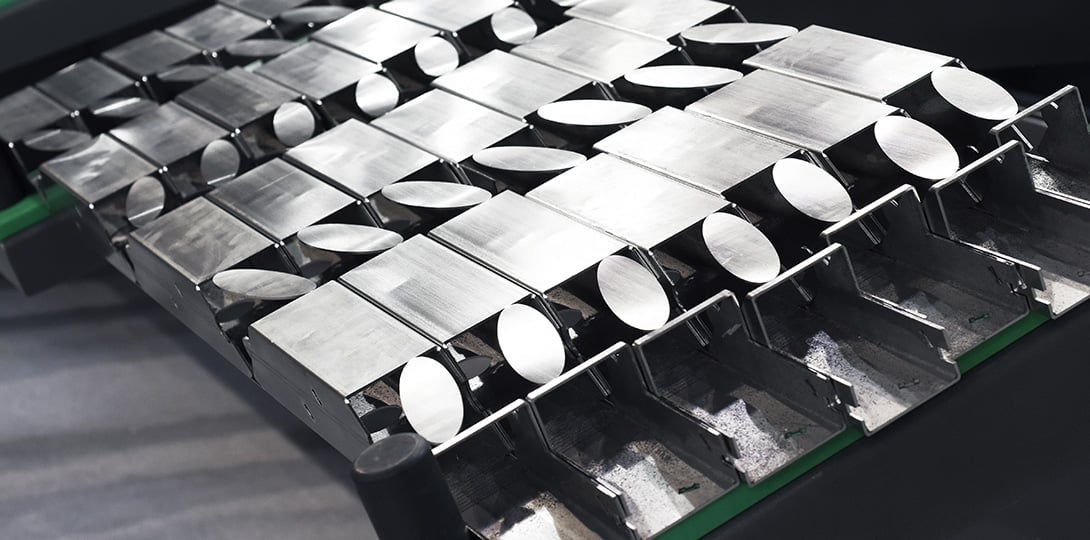
From our blog
When is it useful to bend a tube with a small bending ...
Dimensions, design, geometric requirements and much more; in tube bending being able to achieve a minimum...
27/03/2024
Topic: metalworking
3D laser cutting machines for tubular profiles
3D laser tube cutting machines are revolutionizing the design of steel structures. Thanks to their efficiency,...
29/01/2024
Topic: metalworking
Passing through joinery to build sustainable constructions ...
LASTTS (LASer cutting Technology for Tubular Structures) is the European project that studies the use of...
17/11/2023
Topic: metalworking